Don’t understand basic Aerodynamics interview questions?
You won’t get the Aerospace Engineering job or the job at the Aviation company. Think companies such as Boeing, Delta, Virgin Atlantic, Alaska Airlines, SouthWest, and more.
Knowing basic Aerodynamics is necessary for both for a job interview and for general knowledge as an Aerospace Engineer.
You will not provide value if you don’t understand the concepts of basic aerodynamics interview questions.
Engineering classes go very in depth, but in reality you only need to know the basics.
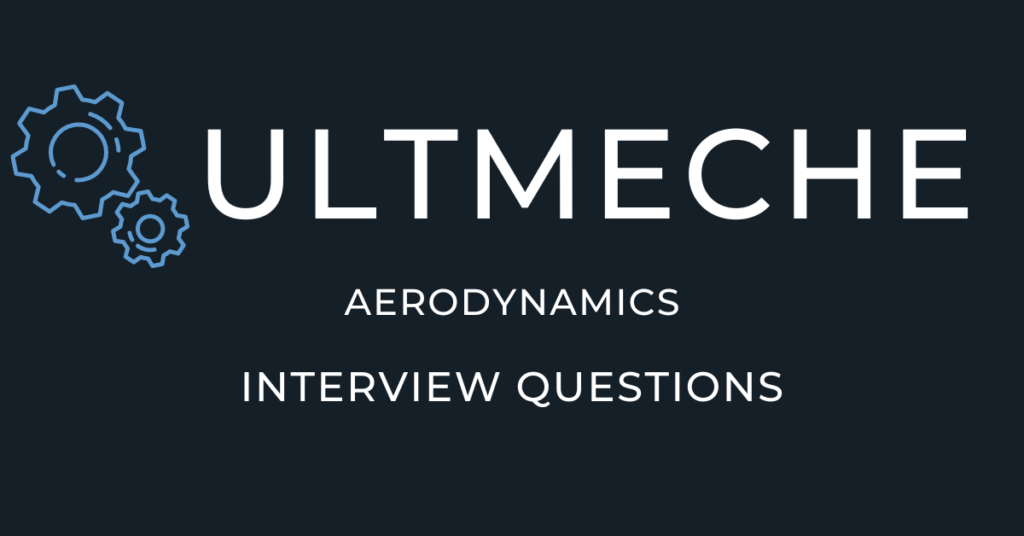
April 20, 2024 by Kazu Fujimoto
The following questions are basic concepts that you will go over in an aerodynamics class.
Make sure you know these questions both so that you are ready for an interview and you also will need to know these terms if you want to be a good aerodynamics engineer.
Book a technical mock interview with Kazu to 10X chances of landing the engineering job.
Can you explain Bernoulli’s principle and it’s relationship to airplane lift?
The Bernoulli principle defines that the increase in fluid speed has an inverse relationship with pressure, leading to a decrease in fluid pressure.
Airplanes are designed with wings that have an airfoil shape – flat at the bottom and curved on top. This geometry makes it so that fluid (air) will split into two streams above and below the wing. The air speed on the upper surface has a longer path, so as a result, causes it to move faster than the bottom surface of the wing.
Per the Bernoulli effect, the increased speed of air above the airfoil results to a higher pressure beneath the wing. The higher pressure at the bottom surface of the wing creates a pressure differential. The pressure difference creates an upward force that is called lift in airplanes. Lift is what allows the airplane to overcome gravity and allow the plane to ascend.
Explain the me the steps you would take to model a CFD of a complex structure
- Determine structure geometry
- Set boundary constraints
- Determine operating conditions
- Apply analysis
- Evaluate results
I would utilize the 5 steps above to model a CFD of a complex structure. I would take a simplified version of the structure geometry and ensure a fine enough mesh to get relatively accurate results. I’d set boundary conditions such as velocity and pressure and also incorporate parameters such as using the correct Reynolds number. I would run the analysis, evaluate the results using engineering judgement, and see iterate as needed until we are satisfied with results or need to change the design.
How do you factor in turbulence in your design for an aerodynamics model?
I’d use the following turbulence models such as the Reynolds-Averaged Navier Stokes to address turbulence in my aerodynamics design.
How is compressibility a factor regarding aerodynamics?
Compressibility is influenced by the Mach number, which is defined as the ratio of speed to the speed of sound. As a general rule of thumb, when it exceeds 0.3, compressibility becomes a factor that needs to be taken into consideration for your aerodynamics design.
The equations we would be looking at would be the Navier-stokes equations. These equations take into consideration parameters such as pressure, velocity, temperature, and density due to compression.
What are the differences between subsonic, sonic, and supersonic flow?
- Subsonic flow – air speed is less than the speed of sound
- Sonic – airspeed occurs at the speed of sound
- Supersonic flow – air speed exceeds the speed of sound (results in shockwaves)
What is a disadvantage of flying an aircraft at supersonic flow?
Supersonic flow occurs when air speed exceeds the speed of sound. A shock wave occurs (which results in a loud BOOM noise that we may hear) and as a result, this causes an increase in drag, requiring more thrust to maintain speed.
What is an advantage of flying an aircraft at supersonic flow?
Although flying in supersonic flow does come with an increase in drag and reduced efficiency, it does allow for faster travel times. Faster travel times can be useful for high speed military aircraft applications.
How is subsonic, sonic, and supersonic flow related regarding an aircraft’s performance?
Subsonic, sonic, and supersonic flow is a characteristic of what aircraft speed is.
Tell me about your familiarity with the Navier-Stokes equations.
I worked in a power generation company where I was responsible for designing turbines. It was necessary to use the Navier-Stokes equations to optimize blade design. Using the Navier-Stokes equations, I was able to simulate airflow over blades over a variety of wind conditions, leading us to optimize blade efficiency and achieve noise reduction. As a result, the design of the turbine led to $10M+ in revenue through product releases. The turbines are a necessary part in the power infrastructure of the Palm Springs desert area.
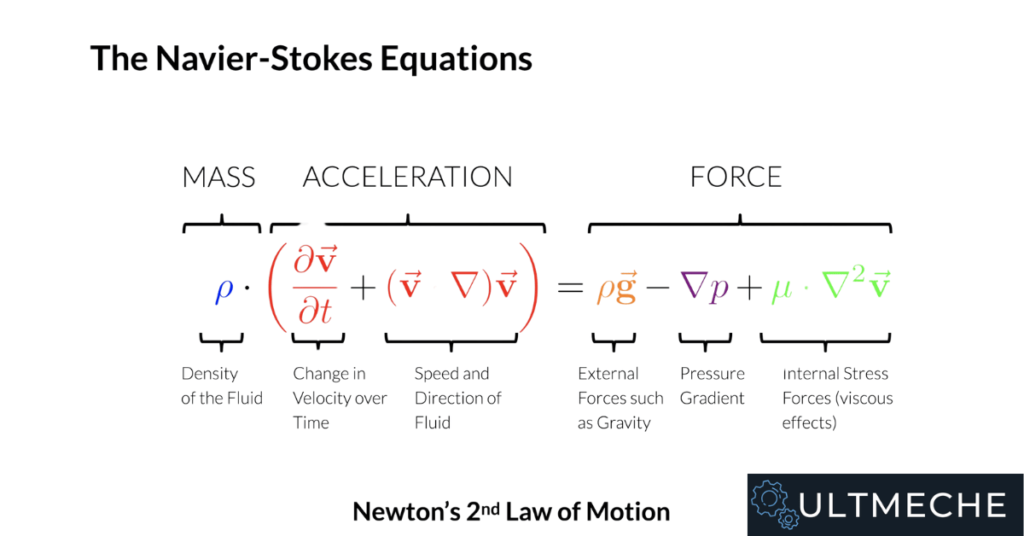
Interviewing Tip – Answer using the STAR Method for Interview Questions whenever possible.
What is ground effect and how does it influence aerodynamics during takeoff and landing?
Ground effect is the change in forces on an aircraft as it approaches a landing surface. The interference of the ground causes a change in airflow patterns around the plan and it plays a huge influence when the aircraft becomes close to the ground (approx 1 wingspan length).
During Takeoff:
Ground effect can be a benefit due to the reduction of drag and allowing the airplane to lift at a lower speed than normally required. This happens as a result of wing downwash, vortex wake, and change in the angle of attack – reducing drag.
During Landing:
When a plane starts descending, there can be a cushioning effect making the aircraft float. As a result of this, it can be difficult for the pilot to make the aircraft touch down at the desired point. Reduced drag from ground effect also can make it so that if the approaching speed is too high, the aircraft may not slow down.
It is important for the pilot to understand these concepts and know how to react in the event of these cases.
How would you design and optimize an aircraft’s shape for maximum efficiency?
Optimizing an aircraft shape should be based on drag reduction and increasing lift. As a designer responsible for commercial aircraft, I was responsible for determining the aircraft shape as the Chief Engineer. It’s important for the body of the aircraft to be streamlined to minimize air resistance. A teardrop-shaped fuselage is pretty standard industrywide and it is known to reduce drag. Wing design is also important and should have a high aspect ratio to lower drag. I led the efforts of our sub teams and oversaw the design, analysis, and testing of aircraft fuselage and wings. This was a very long and arduous effort, but was successful and resulted in $1B+ of commercial aircraft production.
Interviewing Tip – Answer using the STAR Method for Interview Questions whenever possible.
What is Reynold’s number?
Reynold’s number is a dimensionless parameter governed by the following equation:
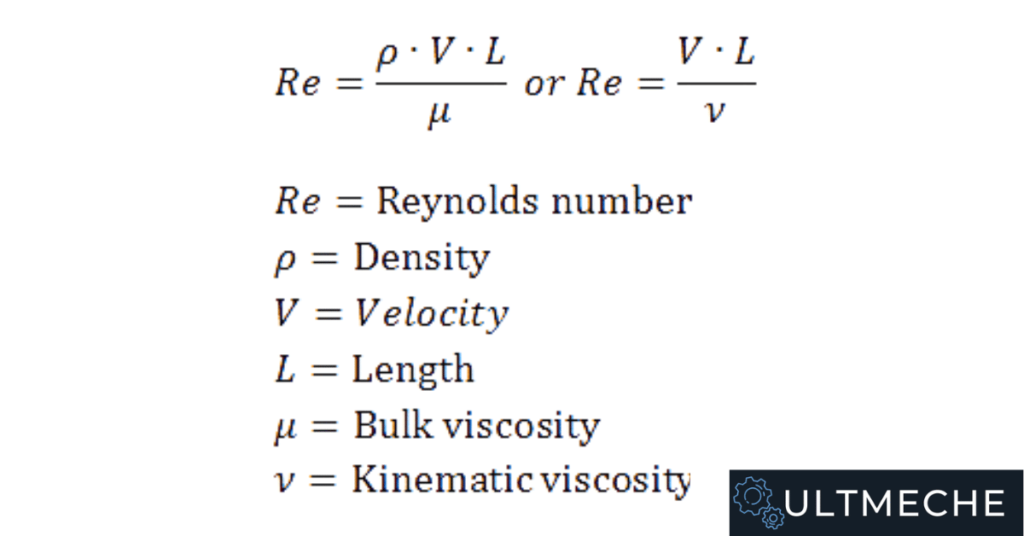
Reynold’s Number describes fluid flow characteristic and relationships to fluid shear and viscosity.
See the different types of fluid flow associated with Reynold’s Number:
- Laminar region: Re < 100
- Transition region: 100 < Re < 10,000
- Turbulent region: Re > 10,000
What is drag coefficient?
The drag coefficient or coefficient of drag is a dimensionless parameter used to describe drag resistance of an object in fluid environment.
What is aspect ratio?
The aspect ratio of a wing is the ratio of it’s span to the mean chord.
It is calculated as the ratio of the square of the wing span to the projected wing area.
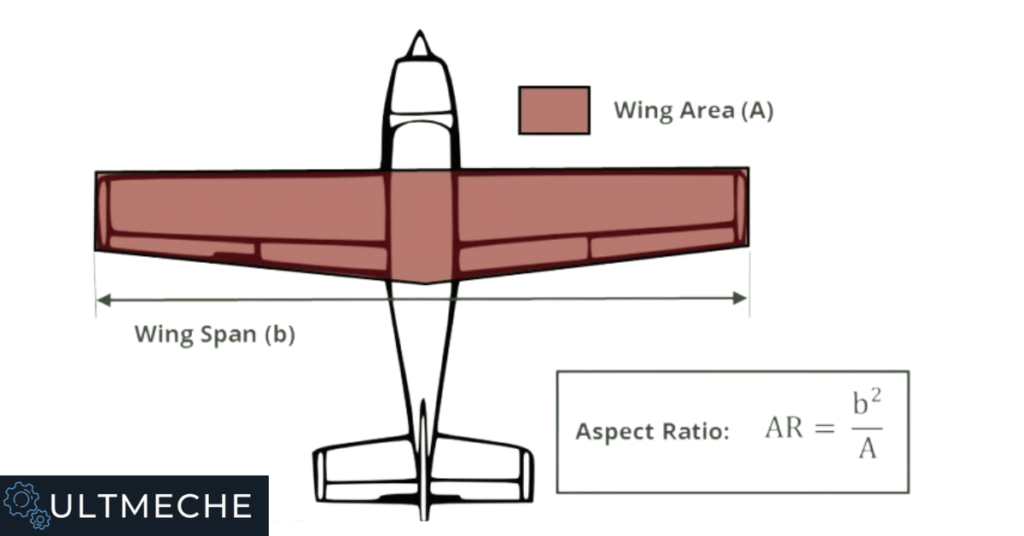
Why is aspect ratio important when it comes to wing design and performance?
A higher aspect ratio would mean the aircraft would experience reduced drag from air pressure differences on the upper and lower surface of the wing during lift. As a result, higher aspect ratio in wing design would mean better fuel economy and longer flight ranges, best for gliders or longer commercial flights.
Explain why wind tunnel testing is so important.
Wing tunnel gives us as Aerodynamics Designers the opportunity to iteratively test a product for its optimal performance, relatively inexpensively. The use of dimensionless parameters allow us to scale testing and determine boundary conditions such as pressure, velocity, temperature and help us determine optimal parameters for geometry to use as a result.
As the team lead, I was responsible for the design, testing, and analysis of the XR-71 winglet. It was due to the company having resources such as a wind tunnel, we were able to iteratively perform testing for this winglet. I oversaw drawings, manufacturing, and the development of documentation such as test plans and procedures for wind tunnel testing. We performed tests over and over and adjusted the design of the winglet geometry until it met industry standards. As a result, this has led the production of the XR-71 military aircraft.
Interviewing Tip – Answer using the STAR Method for Interview Questions whenever possible.
Tell me about your experience using computational methods to analyze and optimize airfoil design.
I was responsible for airfoil design and analysis for my project.
I followed the following steps:
- Determine structure geometry
- Set boundary constraints
- Determine operating conditions
- Apply analysis
- Evaluate results
I created a CAD model and imported that into CFD analysis to get more data regarding pressure, lift, and drag coefficients. This sequence gives us an iterative system to design and determine the optimal wing shape. At the end of our analysis, I used engineering judgement and compared analysis results with theoretical and lab results. When the data started looking valid, I then presented the design to the team through a design review and successfully had it approved by all stakeholders, resulting in $100M+ in product releases.
Have you used ANSYS in aerodynamics design or analysis?
I have used ANSYS to perform CFD on an aircraft structure. I imported a CAD model from Creo and meshed the geometry into smaller elements. Then I defined boundary conditions, material properties, and defined the fluid flow. I then run my analysis and depending on what results come in, I iterate until I come up with a feasible design using engineering judgement.
What are some key design considerations when it comes to supersonic intake and nozzle design?
Key design considerations include the ability to decelerate the air to subsonic speeds before it reaches the engine to minimize pressure loss. This requires accurate shaping of the design of the geometry of the intake duct. The design also needs to take into consideration factors such as speed, altitude, angles, manufacturability, and weight.
Regarding nozzle design, the main goal is to accelerate exhaust gases to convert thermal into kinetic energy. As a result, this requires an expanding duct shape. The dimensions of the nozzle will depend on factors such as height and altitude.
Ultimately, the components need to undergo structural and thermal analysis to ensure functionality.
How does change in air pressure and temperature affect aerodynamic performance of an aircraft?
They have a huge impact on aircraft aerodynamics.
Changes in pressure will change the force exerted on the aircraft, which will then affect lift as a result. Changes in pressure will also result in changes of fluid speed as a function of the Bernoulli principle.
Changes in temperature will also change aerodynamic performance on an aircraft. Temperature has an effect on volume and density. Lower air density will result in reduced lift and engine thrust, which reduce aircraft efficiency as a result. Cooler temperatures will increase air density and increase lift, but may cause increasing drag.
There will generally be a variety of many different parameters so it will be optimal to design and account for air pressure and temperature as a function of speed, altitude, fuel usage, and costs.
How have you implemented drag reduction in your aerodynamic designs?
I’ve been responsible for the design and analysis of determining airflow geometry for several aerodynamics components. As a design engineer for commercial aircraft, I was responsible for design, testing, and analysis. What I did was took a theoretical “napkin sketch”, modeled it in CAD, manufactured the design and performed wind tunnel testing. Using CAD, CFD, I was able to determine what the air flow was over my structure I designed and this allowed me to understand the flow and pressure distribution along the shape. Ultimately, I needed to make smooth surfaces to optimize aerodynamic efficiency.
How would you use code to leverage improvement of aerodynamic designs?
The use of coding and programming can improve the process of aerodynamic design and manufacturing. By designing and writing models through code, this can streamline the entire process all the way from determining geometry all the way to running analysis and determining what the optimal boundary conditions would be.
Coding can greatly assist with things such as reducing data and post processing for internal review and customer validation. Efficient code will allow the use of parametric modeling, which is a very efficient way to go about designing structures.
Walk me through the process of designing an aerodynamic UAV for high altitude applications.
UAVs at high altitude require the operation in an environment in thin air. As a result, this reduced lift and engine performance. A larger wing span will be required due to the fact that UAVs need to be operating at higher altitudes.
In addition to operating in higher altitude will come effects such as lower temperatures, wind patterns, solar radiation exposure, and the requirement for associated communication systems to meet mission requirements.
In summary:
- High altitude – thin air; leads to reduced lift generation and engine performance
- Lower temperatures at high altitude will lead to changes in material properties and associated electrical systems
- Unpredictable wind patterns
- Solar radiation exposure
- Adequate comm systems for communication
How do you validate results of a computational aerodynamics model such as CFD?
Validating the results for a computational aerodynamics model such as CFD will be an iterative process.
The process will undergo a sequence such as:
- Determine structure geometry
- Set boundary constraints
- Determine operating conditions
- Apply analysis
- Evaluate results
- Compare with real time testing such as wind tunnel testing
It will be up to the engineers to design and set the parameters of the experiments such that the model will pass and move to production or fail and be re-analyzed. A prototype of the model may be modeled and tested in an environment such as a wind tunnel.
What are the limitations of validation techniques regarding aerodynamics models?
Limitations of validating aerodynamics models will be constrained to cost, risk, and resources. It is important that the engineering company or firm in question also has to tools and experience necessary to successfully evaluate engineering models using engineering judgement.
Testing such as wind tunnel and flight testing are both expensive and bring forth safety risks. These tests can also be very time consuming and cause impacts to project schedules, which can lead to delays. Schedule delays are very common in the industry and need to be optimized to ensure profitability for a company.
It is up to the engineer to ensure that geometry, boundary conditions, and engineering results of the respective aerodynamics models make sense. Not an easy task to do at all.
Closing Thoughts on Aerodynamics Interview Questions
Aerodynamics is a very fundamental engineering class that will stay throughout your entire career as an aerospace engineer.
There’s so much to cover from fluid mechanics, CFD, airfoil shapes, wing design, and much more.
Use these basic aerodynamics interview questions as a guideline to prepare yourself.
Want to learn how to write a good aerospace engineer resume?
Check out: Aerospace Engineer Resume to 10X chances of landing an interview for Aerospace companies.
Don’t forget to check out our career services as we provide resumes, cover letters, interviews, and LinkedIn optimization for those specializing in engineering careers.
Book a technical mock interview with Kazu to 10X chances of landing the engineering job.
Our mock interviews break up behavioral and technical step by step and as a result will prepare you for challenging interviews.
About the author
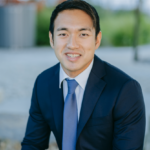
Kazuyoshi Fujimoto, PE
Founder | Engineering Career Coach | Principal Mechanical Engineer
Kazu oversees all of ultmeche’s engineering services. He provides consulting such as resume reviews, rewrites, mock interviews, and all services career related. Additionally, Kazu performs consulting work regarding Oil & Gas, Automotive, and Aerospace & Defense. Kazu is licensed as a professional engineer in the state of California and has 9+ years of experience in Oil & Gas, Automotive, and Aerospace & Defense.
1 thought on “Aerodynamics Interview Questions – Top 25”